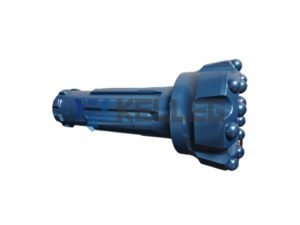
Failure Modes of DTH Drill Bits
Failure mode of DTH drill bit includes the failure of the main body of the drill bit and carbides. Understanding this can help us drill better.
Failure mode of DTH drill bit includes the failure of the main body of the drill bit and carbides. Understanding this can help us drill better.
DTH drill bit is a tool used for geological exploration and mineral extraction, mainly composed of carbide, exhaust hole, head, spline, and impact end face.
DTH drill bit breaks the rock with impact rotation. It creates a crushing pit in one short, then rotates for a second impact and finally forms a blast hole.
A well-designed DTH drill bit is highly beneficial in improving rock drilling efficiency, and the selection of materials is an important factor.
Factors that affect the drilling effectiveness of hydraulic rock drills include rock drilling speed and rock breaking effectiveness.
The service life of button bit affects the cost and efficiency of rock drilling. The 5 aspects of this article can improve the service life of button bit.
Carbide is an important part of button bit. Understanding of the selection principle of carbide can assist in improving rock drilling efficiency.
This article mainly introduces the structure of DTH drill bit. Manufacturers can further prolong its service life by studying the structure of DTH drill bit.
Welding technology can be developed and perfected through brazing technology, surface modification technology, rock drill bit materials and brazing automation.
In coal mining engineering, we can choose rock drill bits reasonably according to the geographical environment.
The important parameters of button bits mainly include geometric parameters, determination of powder discharge groove, button parameters and water outlet holes.
The management of the heat treatment process of rock drilling tools can start with the management of employees and equipment.
Analyzing the possible quality problems of rock drill bit will help manufacturers formulate improvement measures and prolong the service life of rock drill bit.
Proper use of button bits can improve engineering efficiency, extend service life and reduce maintenance costs.
Proper heat treatment is essential to ensure the strength, toughness and durability of threaded extension rods.
The common failure modes of mining tri-cone bits include bearing failure, cutting structure failure, cone shell wear, and gauge structure damage.
This article mainly describes the factors that affect the quality stability of drill rods, mainly including materials, processes and equipment.
Heat treatment is an important process in the manufacturing and production of rock drilling tools, which plays a decisive role in improving their inherent quality and service life.
The correct use and grinding of button bits is an important means to improve engineering efficiency, and also a key measure to extend their service life.
To deal with the failure modes of button bit cemented carbide, we need to start from many aspects such as wear, heat treatment, and fracture of various parts.
China Reliable Rock Drilling Tools Supplier, Free Samples Available.