In drilling, damage or fracture will occur in the shank, shank shoulder, and body of drill rod, shank shoulder, and body of drill rod. Fatigue fracture refers to the phenomenon that when materials are under cyclic stress and micro-cracks gradually occur in local high-stress concentration areas, and as the stress continues to act, the cracks expand steadily, eventually leading to overall fracture. For drill rods, fatigue fracture is also one of the frequent failure forms.
The fatigue breakage at 200~400mm before shank shoulder is usually called “normal failure” of drill rod, and the breakage or brittle breakage in other parts is called “abnormal failure”. Fracture is the natural phenomenon of separation of two adjacent parts of the metal material locally or in the whole section when the force reaches a certain value under the action of external force. In practical engineering, the complete fracture of metal material is usually called fracture, and the local fracture of metal material is called crack.
The factors affecting manufacture and rock drilling of drill rods are complex, and the causes of breakage are also multifaceted. It often requires scientific and rigorous analysis of the chemical composition of raw materials, rolling state, manufacturing process, geometric structure, surface quality, mechanical properties, microstructure, and applicable conditions of rock drilling, as well as macroscopic and microscopic characteristics of fracture. What are the characteristics of the fatigue fracture of drill rod?
Macroscopically
Shank shoulder root fracture
Fracture characteristics
There are two characteristics, one is a fatigue fracture and has multiple fatigue source points around the fracture. The other is a brittle fracture, and the source point of crack occurs mostly in the corner.
Reason
①Radius of the transition arc of shank shoulder
At the root of shank shoulder, stress concentration is easy to occur near the transition arc due to the sudden change of the geometric shape section of shank shoulder.
②Forging quality
Forging quality has a great influence on service life of shank shoulder roots. When mold is used to a hot state to a certain extent, its hardness decreases, and local deformation occurs.
③ Heat treatment process
To eliminate the “metallurgical gap” caused by the forging process of shank shoulder, induction heating and normalizing should be carried out after forging. During the heating, to ensure that the large section of shank shoulder is not overheated, a low-temperature zone will appear at the root and front of shank shoulder. Such normalizing treatment becomes a high-temperature tempering state. If the hardness is reduced, the yield point and normal fracture resistance are reduced, which creates conditions for brittle normal fracture failure.
④Quality of rock drill rotating sleeve
Rock drill rotating sleeve is a vulnerable part. Especially after using it for some time, the size of hexagonal inner hole of sleeve is large after wear. On the other hand, inner chamfer of rock drill rotating sleeve is a straight chamfer, not a circular chamfer, which cuts the two sides of the transition arc into sharp dents when repeatedly impacting the root of shank shoulder. This indentation aggravates the stress concentration.
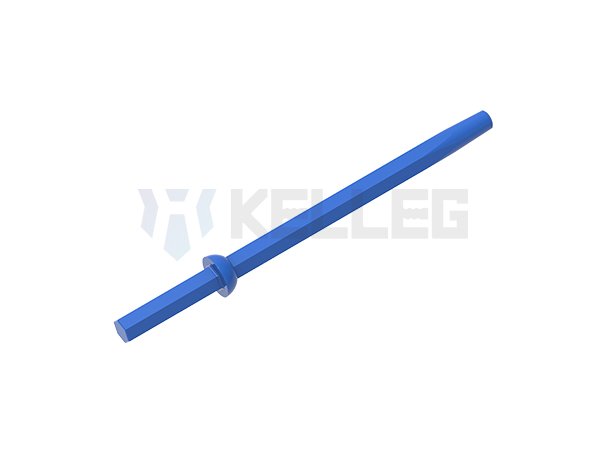
Middle of shank shoulder is broken
Fracture characteristics
Usually, the fracture in the middle of shank shoulder is an internal fatigue fracture. The fracture is smooth.
Reason
①Inner hole diameter sudden change
During forming of shank shoulder, free upsetting deformation occurs first, and the diameter of inner hole increases with the increase of outer diameter of shank shoulder. Then, when upsetting metal part touches the inner cavity wall of mold, the flow of metal to outside receives obstruction and changes to direction of an inner hole with less resistance, resulting in thickening of wall thickness and a reduction of inner hole diameter.
②Iner tube is poorly bonded to base steel, and inner hole forms a trumpet shape
In drilling, a local upsetting of liner tube forces a “flared” hole to form in the middle of shank shoulder. The “flared” water hole is easy to cause strong stress concentration, coupled with a decarburization layer on an inner wall of base, and will lead to fatigue strength is reduced. Under the action of tensile (compressive) stress, a fatigue crack source is generated, which propagates radially outward into the matrix steel.
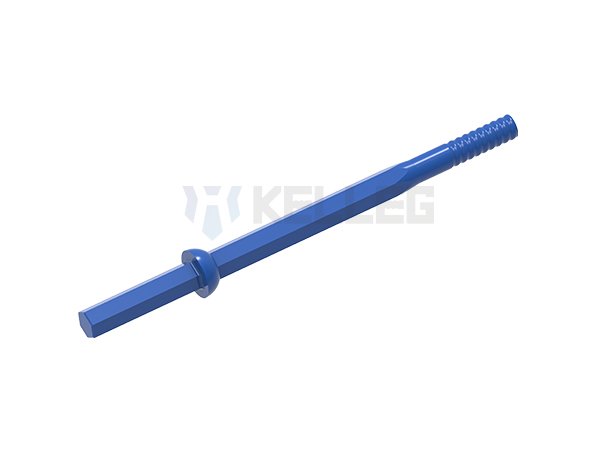
Microscopically
Metallographic organization
Fracture characteristics
Fatigue cracks start from inner hole and expand outward, fatigue arc band is visible, and there are more visible steps.
Microscopic fracture
Observing fracture of drill rod under a scanning electron microscope, fatigue streaks in the fatigue zone are not visible but showed friction traces in different degrees.
How to analyze the fatigue fracture of drill rods?
How do we analyze and study the causes of fatigue fracture of drill rods?
Material composition and organizational structure analysis
Through chemical composition analysis, observe whether the composition of the material meets the design requirements. At the same time, observe the material’s internal structure through metallographic examination and check whether there are microstructures such as martensite and bainite and the distribution and shape of these tissues.
Macroscopic inspection
Perform a visual examination of the fractured drill rod, focusing on its overall appearance, dimensions, and the precise site of the fracture. Also, be attentive to any additional damage or remnants near the fracture. This data is instrumental in ascertaining the character and origins of the drill rod’s breakage.
Fatigue source analysis
Find the location of the fatigue source on the fracture surface and analyze the cause of its formation. For example, fatigue sources may result from surface defects, internal stress concentration, local corrosion, or fatigue cracks in the material.
Stress Analysis
Using finite element stress analysis and other methods, calculate the stress distribution of drill rods in the working environment, find the stress concentration areas, and observe whether fatigue cracks or other damages exist.
Work environment analysis
Understand the working environment of the drill rod, including operating temperature, humidity, pressure, corrosive media, and other factors, and analyze the impact of these factors on the fatigue fracture of the drill rod.
Comprehensive analysis
A thorough examination of the preceding information, in conjunction with factors like material composition, organizational structure, working conditions, and more, to provide a comprehensive assessment of the underlying reasons behind the fatigue fracture of the drill rod.
Building on this foundation, we can propose corresponding measures for prevention and improvement. These may include optimizing the material composition and organizational structure, enhancing the working environment, bolstering equipment maintenance and upkeep, and enhancing manufacturing and processing quality to mitigate the occurrence of fatigue fractures in drill rods.
In summary, the fatigue fracture surface of the drill rod exhibits distinct characteristics. By carefully observing and analyzing these traits, we can effectively determine the root causes and the sequence of events leading to fatigue fractures in drill rods. It not only enhances our understanding of the operational performance and failure mechanisms of drill rods but also helps us to prevent and reduce the fatigue fracture phenomenon of drill rods in the design and manufacturing process. Simultaneously, to manufacture high-quality drill rods, manufacturers must exercise strict control over every facet of material selection, processing, shaping, and heat treatment. Through a detailed and scientifically rigorous analysis of the fatigue fracture surface, we continually refine our processes and material selection methods, ultimately extending the lifespan of drill rods.