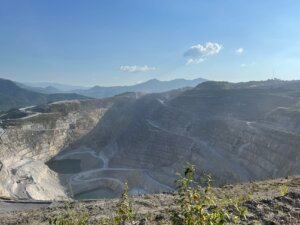
What innovations has high-efficiency crushing and separation technology brought to open-pit mining?
Discover how high-efficiency crushing and separation technology is transforming open-pit mining with improved recovery, lower energy use, and greener operations.