As mineral resources become increasingly vital to the global economy, the efficiency and sustainability of open-pit metal mining have become key concerns both within and outside the industry. Traditional mining methods face multiple challenges, including low efficiency, high costs, and environmental pollution. However, the introduction of modern mining technologies has injected new vitality into this sector. These innovations not only significantly improve mining efficiency and reduce costs but also minimize environmental impact, promoting sustainable development in open-pit metal mines. This article will explore the specific applications of modern mining technology in open-pit metal mines, revealing how it can improve mining efficiency, reduce costs, and promote the transition of mines toward intelligent and green operations.
Automation Equipment Application
Automated Drilling Machines
Traditional drilling operations rely on manual labor, resulting in low efficiency, excessive drill bit wear, and energy waste. Modern automated drilling rigs, equipped with advanced devices such as pressure sensors, temperature sensors, and vibration sensors, have achieved automation and intelligence in the drilling process. These rigs can adjust drilling parameters in real-time based on data, ensuring drilling accuracy and efficiency. Statistics show that after adopting automated drilling rigs, mining efficiency has increased by 20%, drilling wear has decreased by 30%, and energy consumption has been reduced by 15%. It not only significantly improves mining efficiency but also lowers operational costs, creating greater economic benefits for businesses.
Autonomous Haulage Trucks
Autonomous haul trucks are another major innovation in modern mining technology. These trucks are equipped with high-precision GPS systems, laser radar, and AI technology, enabling them to navigate and avoid obstacles autonomously in complex mining environments. Autonomous trucks not only improve transportation efficiency but also significantly reduce labor costs and accident risks. It is reported that mines using autonomous haul trucks have seen a 30% increase in transport efficiency and a 50% decrease in accident rates.
Automated Loading Equipment
Automated loading equipment uses high-precision cameras and image recognition technology to quickly and accurately load ore into transport vehicles. These systems can recognize ore types, sizes, and positions in real-time and carry out precise operations according to preset loading strategies. Compared to traditional manual loading methods, automated loading equipment not only increases loading efficiency but also drastically reduces labor costs and operational errors. Statistics show that after the adoption of automated loading equipment, loading efficiency increased by 25%, labor costs were reduced by 40%, and error rates dropped by 50%.
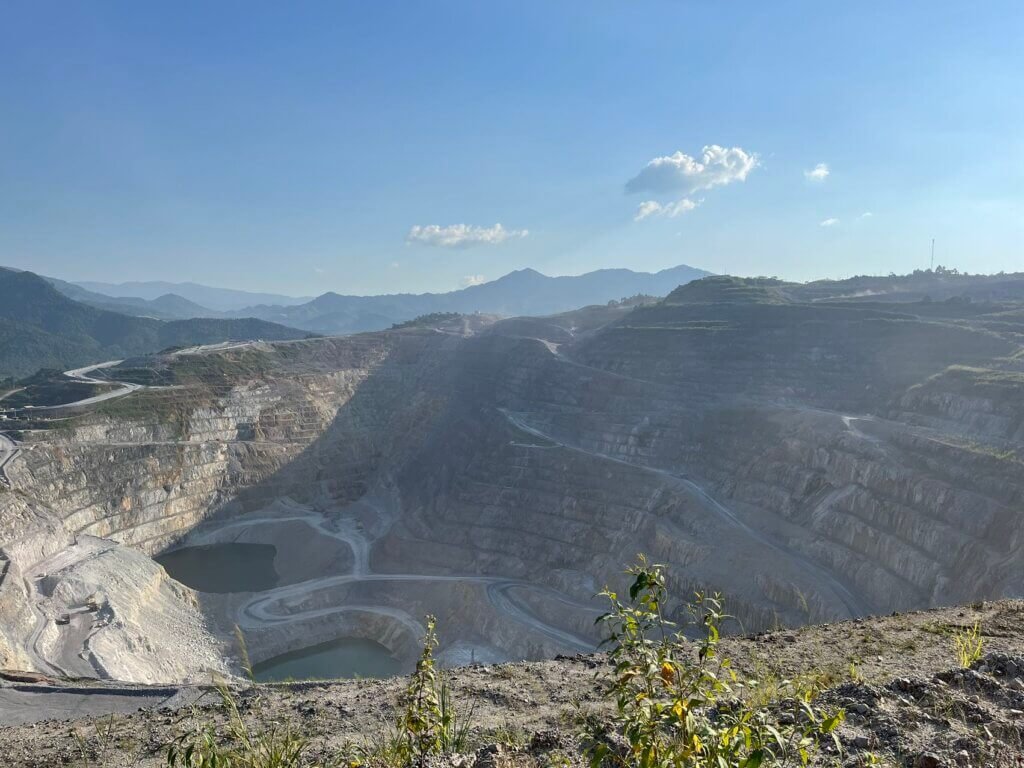
Digital Management Application
3D Mining Modeling
Using lidar and drone aerial photography technology, it is possible to quickly and accurately construct a three-dimensional digital model of a mine. This model not only helps engineers to intuitively understand the terrain, geological structure, and resource distribution of the mine but can also be updated in real-time during the mining process to reflect the latest status of the mine. Through the three-dimensional model, managers can accurately calculate ore reserves, formulate more scientific mining plans, and avoid over-mining or resource waste.
Real-Time Data Collection and Analysis
Through sensors and IoT technology, real-time data on equipment operations, environmental conditions, and ore quality can be collected and transmitted to the dispatch center. Big data analytics enable managers to identify issues and formulate effective countermeasures. For example, by analyzing equipment operational parameters, the system can predict failure risks and schedule maintenance in advance, reducing losses due to equipment downtime.
Digital Dispatch System
The digital dispatch system integrates GPS, GIS, and AI technologies for the intelligent scheduling of equipment, vehicles, and personnel within the mine. The system automatically assigns tasks based on real-time production conditions, optimizing employee schedules and material allocation to ensure improved production efficiency. Additionally, smart scheduling effectively reduces equipment idle time, lowering operational costs and resource wastage.
Green Mining Technologies
Water Resource Management
In water-scarce areas, modern mines employ technologies such as rainwater collection, wastewater treatment, and reuse to effectively manage water resources. Mine set up rainwater collection systems to capture and process rainwater for use in mining, dust suppression, and greening, reducing reliance on groundwater and surface water while lowering water consumption. Additionally, wastewater treatment and reuse technologies ensure the safe discharge or recycling of wastewater, further conserving water resources.
Dust Control Technologies
Modern mines use measures such as misting, dust control covering, and vegetation restoration to effectively control dust pollution from mining activities. Misting devices are installed in areas prone to dust generation, such as ore crushing, transportation, and storage, to use high-pressure water spray to adsorb dust particles and reduce dust concentration in the atmosphere. Dust control covering measures use methods such as dust control nets, solidifiers, or plant coverings to prevent dust generation and protect the surrounding environment and the health of residents.
Tailings Management Technologies
Tailings are a significant waste product of mining operations, and traditional disposal methods consume large amounts of land and cause environmental pollution. Modern mining techniques, such as dry tailings discharge, tailings backfill, and comprehensive utilization, solve many of the disposal challenges. Tailings can be used for backfilling, road construction, or as building materials, reducing the space occupied by tailings ponds and mitigating dam collapse risks. The backfill process supports the surrounding rock and prevents collapse, reducing surface environmental damage. Comprehensive utilization techniques recover valuable minerals from tailings, maximizing resource use.
Conclusion
The application of modern mining technology in metal open-pit mines not only signifies a significant improvement in mining efficiency and resource utilization but also marks a crucial milestone in the mining industry’s transition toward intelligent and green operations. As technology continues to evolve and be applied more extensively, we have every reason to believe that future metal open-pit mines will be more efficient, safer, and environmentally friendly. By actively embracing and promoting these advanced technologies, mining companies can not only maximize economic benefits but also play a crucial role in balancing global resource development and environmental protection, collectively shaping a sustainable future for the mining industry.